Significance of employee engagement activities in manufacturing industry 2024
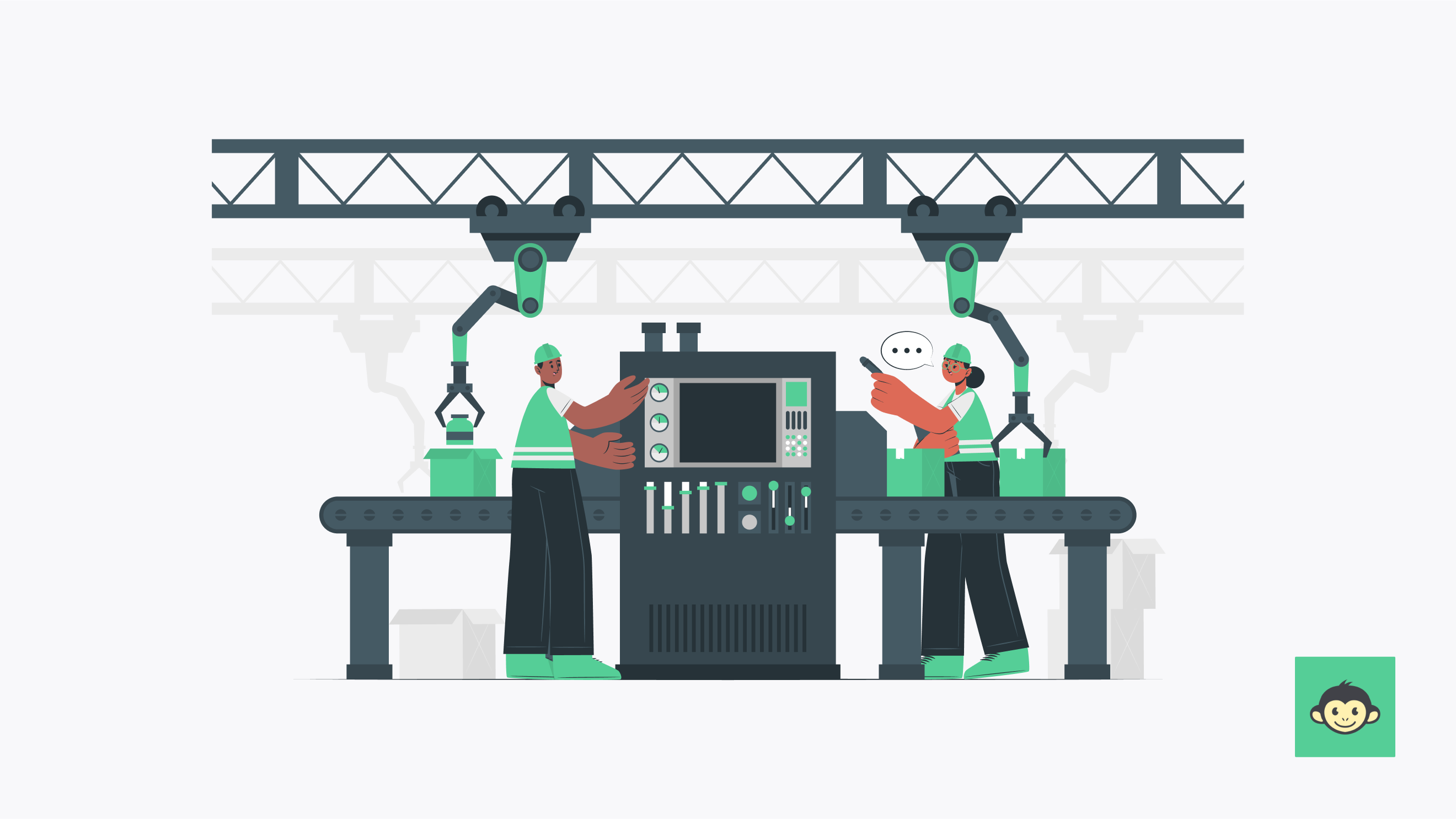
Imagine your factory buzzing not just with the hum of machinery but with the palpable energy of a team that's not just present but passionately involved. We're not talking about the tired "trust falls" of yesteryears – we're diving into a world where engagement is taken care of, and your workforce is the ensemble cast of blockbuster production.
Now, if you're wondering why bother, let me tell you – engaged employees aren't just clock-watchers; they're the maestros orchestrating the symphony of production. And guess what?
The wand that transforms your workforce into a synchronized, high-performing orchestra is none other than simple but mindful employee engagement activities.
What is employee engagement in manufacturing?
Employee engagement in manufacturing refers to the extent to which employees in the manufacturing industry are emotionally invested, motivated, and committed to their work and the goals of the organization.
It goes beyond the simple act of being physically present at work; instead, it focuses on creating an environment where employees feel a genuine emotional connection to their work, their colleagues, and the overall mission of the company.
To foster employee engagement in manufacturing, organizations often implement various strategies, including regular communication, training and development opportunities, recognition programs, and the use of technology, such as employee engagement software, to gather feedback and measure engagement levels.
Why is improving employee engagement important in manufacturing?
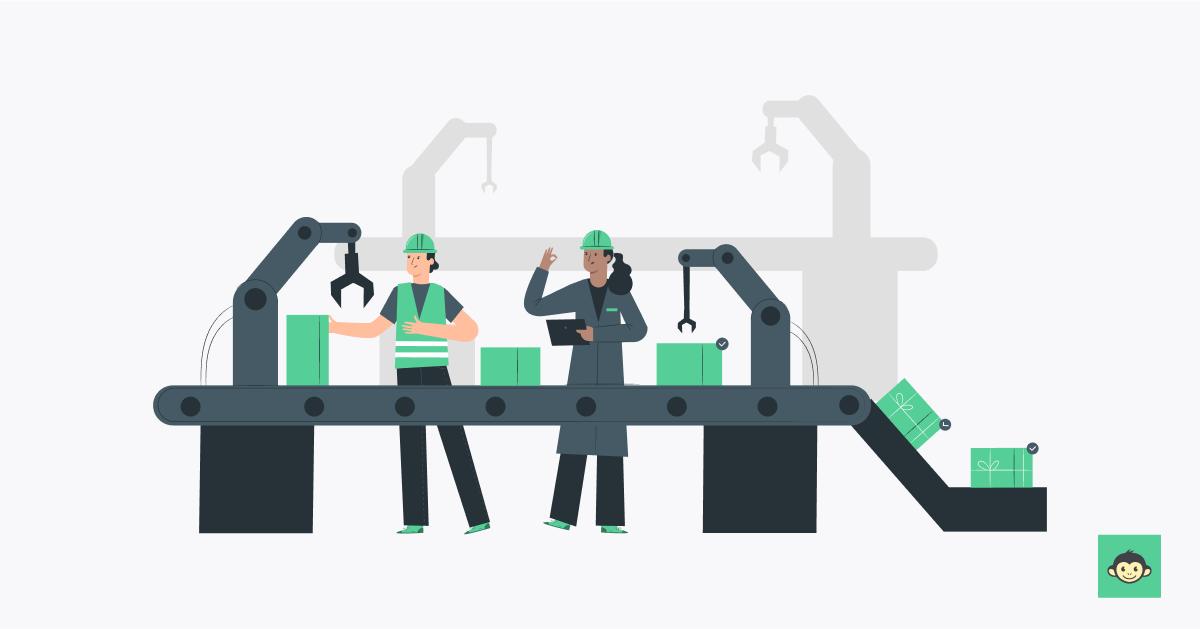
In the manufacturing sector, where the work often involves repetitive tasks and the use of machinery, fostering employee engagement is crucial for several reasons:
- Productivity: Engaged employees are more likely to be productive. When workers feel connected to their tasks and understand the significance of their contributions, they are motivated to perform at their best.
- Quality: A workforce that is engaged is more likely to pay attention to detail and take pride in the quality of their work. This can lead to improved product quality and a reduction in defects.
- Innovation: Engaged employees are more likely to contribute ideas and be proactive in suggesting improvements to processes. This can be particularly valuable in a manufacturing setting where efficiency and innovation are key to staying competitive.
- Employee retention: Manufacturing operations often require skilled workers, and retaining these skilled employees is essential. Engaged employees are more likely to stay with a company, reducing turnover and the associated costs of recruitment and training.
- Safety: Engaged manufacturing employees work and are more likely to adhere to safety protocols and guidelines, reducing the likelihood of accidents and injuries in a manufacturing environment. On average the industry suffers from 400,000 fatal injuries, which is a lot.
5 Employee engagement trends in manufacturing
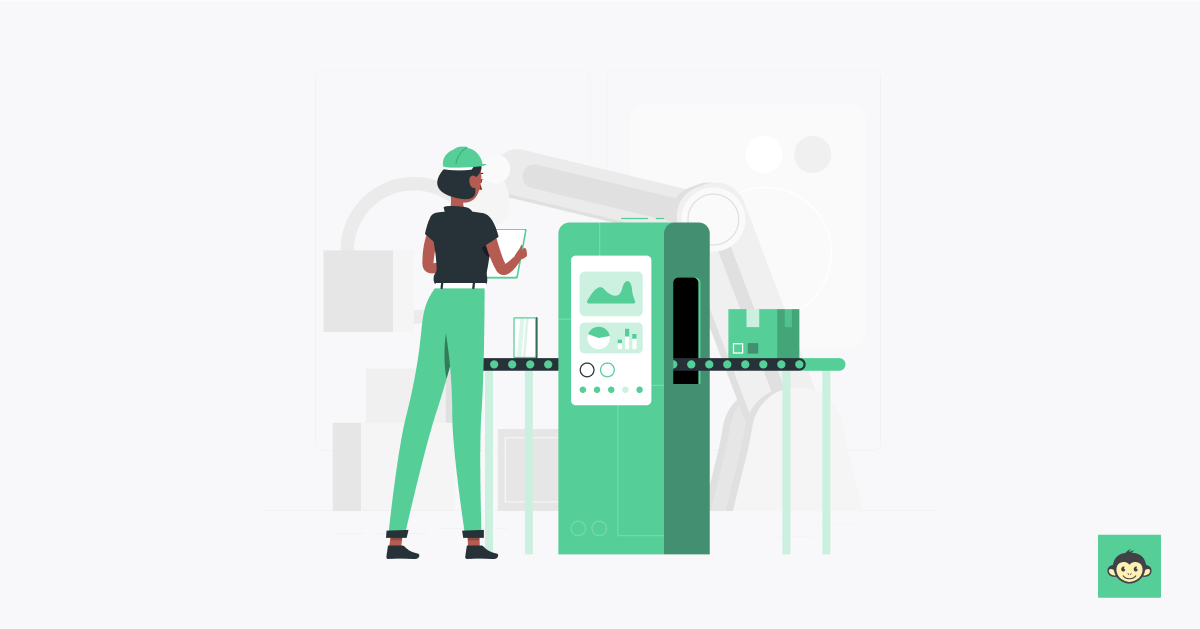
Remember that the landscape of employee engagement is dynamic, and trends may shift based on industry developments, technological advancements, and societal changes. Here are five employee engagement ideas that have recently caught on.
1. Technology integration
Manufacturing companies are increasingly leveraging technology to enhance employee engagement. This includes the use of employee engagement software, mobile apps, and communication platforms to streamline internal communication, provide real-time feedback, and recognize employee achievements.
Integration of technologies like augmented reality (AR) and virtual reality (VR) for training and skill development can also contribute to increasing employee engagement.
2. Remote work adaptation
The COVID-19 pandemic accelerated the adoption of remote work practices, even in the manufacturing sector. While not all manufacturing roles can be performed remotely, some functions, such as administrative tasks, planning, and certain aspects of quality control, can be done off-site.
Employee engagement strategies need to adapt to this hybrid work environment, ensuring that remote and on-site manufacturing workers feel equally connected and engaged.
3. Focus on well-being
Employee well-being is gaining prominence in manufacturing. This involves not only physical safety on the shop floor but also attention to the mental and emotional well-being of corporate employees.
Companies are implementing wellness programs, mental health resources, and flexible work arrangements to support their employees' overall health.
4. Personalized employee experiences
Recognizing that each employee is unique, manufacturing companies are moving toward more personalized employee experiences.
This involves tailoring training programs, career development plans, and recognition efforts to individual preferences and career goals. Personalization contributes to a sense of value and belonging among employees.
5. Continuous learning and development
With the rapid advancements in technology, manufacturing employees need to update their skills continually. Companies are investing in continuous learning and development programs to upskill their workforce.
This not only enhances employee engagement by providing growth opportunities but also ensures that the workforce remains adaptable to technological changes in the industry.
11 Common obstacles to frontline employee engagement
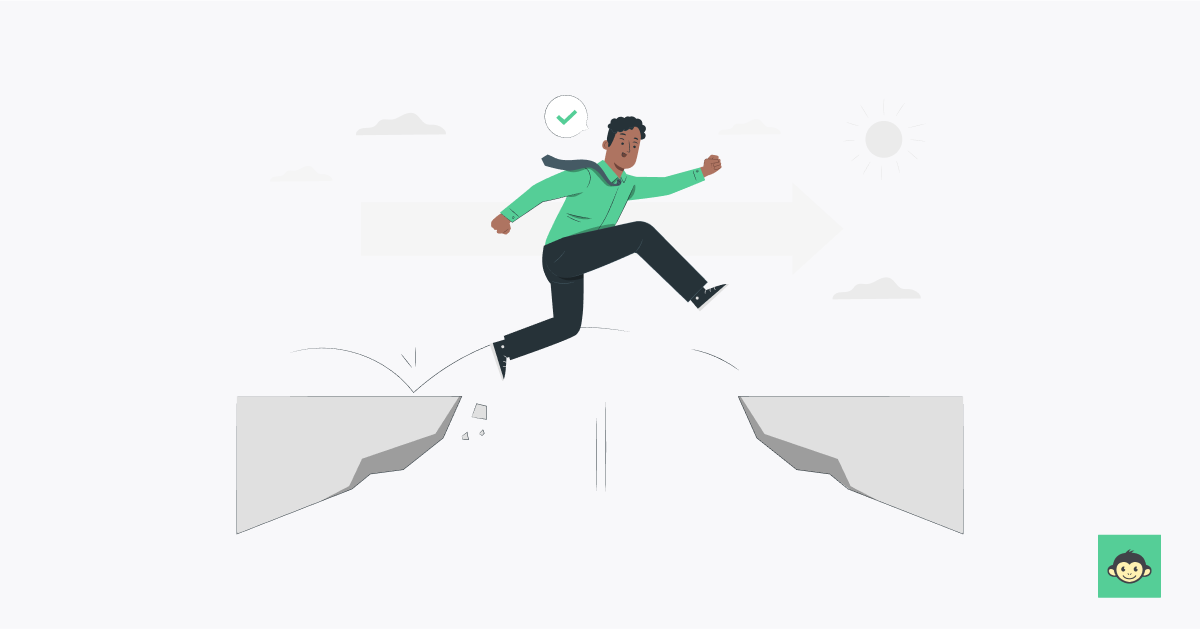
Frontline employee engagement is essential for the success of any organization, especially in sectors like manufacturing, where the workforce is often at the forefront of operations.
However, various obstacles can hinder effective engagement. Here are 11 common challenges faced by organizations in engaging their frontline employees:
- Lack of communication: Insufficient or ineffective communication channels can lead to misunderstandings, decreased morale, and a sense of disconnection among frontline employees.
- Limited recognition: Frontline workers often feel undervalued if their contributions are not recognized. Lack of acknowledgment for hard work and achievements can result in decreased motivation.
- Inadequate training and development: Insufficient training opportunities or a lack of clear career development paths can make frontline employees feel stagnant in their roles, leading to disengagement.
- Safety concerns: In manufacturing and other industries, safety is paramount. Frontline employees might disengage if they feel that safety concerns are not adequately addressed or if they don't have the proper tools and training.
- Limited autonomy: Micro-management and a lack of autonomy can make employees feel disempowered and disengaged. Frontline workers often appreciate having some level of control over their work.
- Absence of feedback: Regular feedback is crucial for employee growth and engagement. Without constructive feedback, frontline employees may not understand how well they're performing or where they can improve.
- Technological barriers: Outdated or complex technology can hinder productivity and engagement. Frontline employees may become frustrated if they struggle with tools and systems that are not user-friendly.
- Limited recognition for skill development: If employees invest time in acquiring new skills or certifications and their efforts go unrecognized, they may lose motivation to continue developing themselves.
- Unclear goals and expectations: Frontline employees need clear goals and expectations to understand their role in achieving organizational objectives. Lack of clarity can lead to confusion and disengagement.
- Work-life balance issues: Frontline roles, especially in manufacturing, may involve demanding schedules. If there's a lack of consideration for work-life balance, employees may experience burnout and disengagement.
- Limited opportunities for advancement: Frontline employees who perceive a lack of growth opportunities within the organization may become more disengaged employees. A clear career progression path is essential for retaining and motivating talent.
How to approach an employee engagement strategy for manufacturing organizations
Crafting an effective employee engagement strategy for manufacturing organizations requires a tailored approach that recognizes the unique dynamics of the industry. Begin by fostering a culture of open communication, ensuring that information flows seamlessly from top management to the frontline workers.
Regular town hall meetings, employee feedback call sessions, and accessible communication channels can bridge the gap between leadership and the shop floor.
Recognition also plays a pivotal role in the engagement of manufacturing employees. You can implement robust recognition programs that acknowledge individual and team achievements.
Whether it's hitting production targets or suggesting process improvements, recognizing these contributions creates a sense of pride and motivates continuous effort.
It’s also wise to invest in comprehensive training and development programs, ensuring that employees have the skills to adapt to evolving technologies. This not only enhances their job satisfaction but also positions them as valuable assets within the organization. Additionally, provides opportunities for career advancement, signaling to employees that their career growth is also a priority.
Safety is paramount in manufacturing. Prioritize safety protocols and equipment and actively involve employees in creating and maintaining a safe working environment. Finally, leverage technology for employee engagement.
From user-friendly communication platforms to specialized manufacturing software, technology can streamline processes and enhance the overall employee experience.
By combining these elements, a robust employee engagement strategy can transform a manufacturing company and workforce into a motivated, skilled, and safety-conscious team.
10 Ways to measure & improve frontline employee engagement the right way
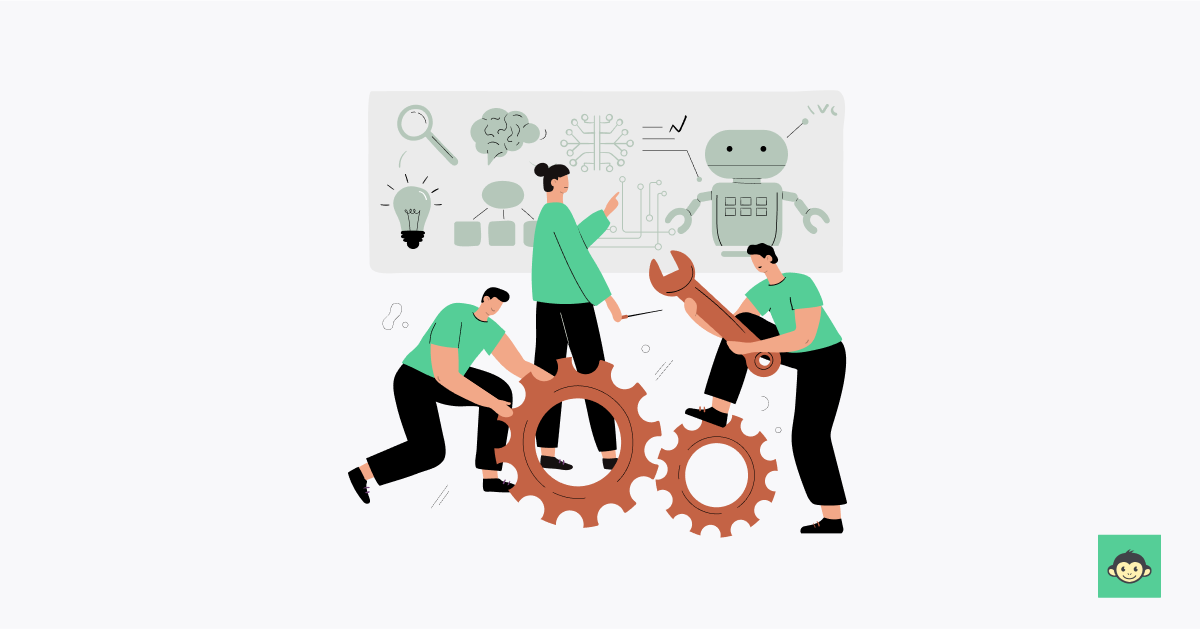
Measuring and improving frontline employee engagement is essential for the success of any organization. Here are 10 effective ways to gauge and enhance engagement among frontline employees:
- Regular surveys and feedback: Implement periodic surveys to gather feedback on job satisfaction, communication effectiveness, and overall engagement levels. Use the insights to identify specific areas for improvement.
- Key performance indicators (KPIs): Define and track relevant KPIs such as productivity, quality metrics, and attendance. Analyzing these indicators provides tangible measures of employee contribution and engagement.
- Recognition programs: Establish robust recognition programs that acknowledge and even reward employees for outstanding performance. Publicly recognizing achievements fosters a positive work environment and reinforces a culture of appreciation.
- Training and development metrics: Monitor participation in training programs and track skill development. A workforce that is continuously learning and evolving is likely more engaged and invested in their roles.
- Employee turnover rates: High turnover can be indicative of disengagement. Monitor turnover rates, especially in critical frontline positions, and investigate the reasons behind departures to address underlying issues.
- Absence and attendance patterns: Analyze absenteeism and attendance patterns. Consistent absenteeism may suggest underlying issues with employee health, job satisfaction, or workplace conditions.
- Peer-to-peer recognition: Facilitate a culture of peer recognition where colleagues can appreciate each other's contributions. This not only boosts morale but also strengthens team bonds.
- Communication effectiveness: Evaluate the effectiveness of communication channels. Ensure that information flows seamlessly from top management to the frontline, and solicit feedback to address any communication gaps.
- Employee surveys on well-being: In addition to engagement surveys, assess employee well-being. Include questions about work-life balance, stress levels, and overall physical and mental health to understand the holistic employee experience.
- Continuous improvement initiatives: Act on the feedback received. Implement changes based on survey results, recognize areas of improvement, and communicate the progress. Demonstrating that employee input leads to continuous process and positive change enhances engagement.
Significance of employee engagement activities in the manufacturing industry
The significance of employee engagement activities in the manufacturing industry cannot be overstated. It's not just about clocking in and out; it's about igniting a spark on the factory floor that transcends the hum of machinery. Engaged employees are the unsung heroes orchestrating the symphony of production, turning routine tasks into a choreography of efficiency.
Picture this: a workforce not merely present but passionately involved, a team where the assembly line becomes a stage for collaboration and innovation. Employee engagement in manufacturing is what transforms a group of individuals into a cohesive unit aligned with the company goals common goal of excellence.
Beyond the clichés of team-building, employee engagement activities in manufacturing are about recognizing the unsung feats – the seamless coordination, the problem-solving prowess, and the daily victories over production challenges.
It's about creating an environment where each worker feels not just a part of the machinery but an integral contributor to the larger narrative of success. It also helps keep their mental health in check.
In fact, the 2023 State of Employee Safety Report shows that mental health is the second most important priority at work, with 77% of employees saying it is extremely important to them.
In the manufacturing tapestry of 2024, engagement activities are the brushstrokes that add vibrancy to the canvas. It's the training programs that empower employees with new skills, the recognition ceremonies that celebrate achievements, and the channels of communication that bridge the gap between the shop floor and the boardroom.
Safety, innovation, and productivity – these pillars of manufacturing prosperity are intricately linked to engaged employees. When workers feel valued, heard, and recognized, they don't just meet targets; they exceed them. They don't just follow processes; they innovate and optimize.
How do you keep manufacturing employees engaged?
Keeping employees engaged requires a blend of communication, recognition, and support. Establishing open communication channels ensures that information flows transparently between management and frontline workers, fostering a sense of inclusion.
Recognition programs also play a pivotal role in celebrating achievements and contributions, while continuous training and skill development empower employees to adapt to evolving technologies. You must also prioritize a safety-first culture and promote work-life balance, contributing to a healthier and more engaged workforce.
Team-building activities and flexible schedules are also beneficial and strengthen bonds among employees, enhancing morale.
Providing autonomy in roles, outlining clear career paths, and utilizing technology for efficiency showcase a commitment to employee growth and satisfaction.
By combining these strategies, manufacturing organizations create an environment where employees feel valued and are not just part of the process but are motivated contributors to the company's success.
How can employee engagement software come in handy for manufacturing companies?
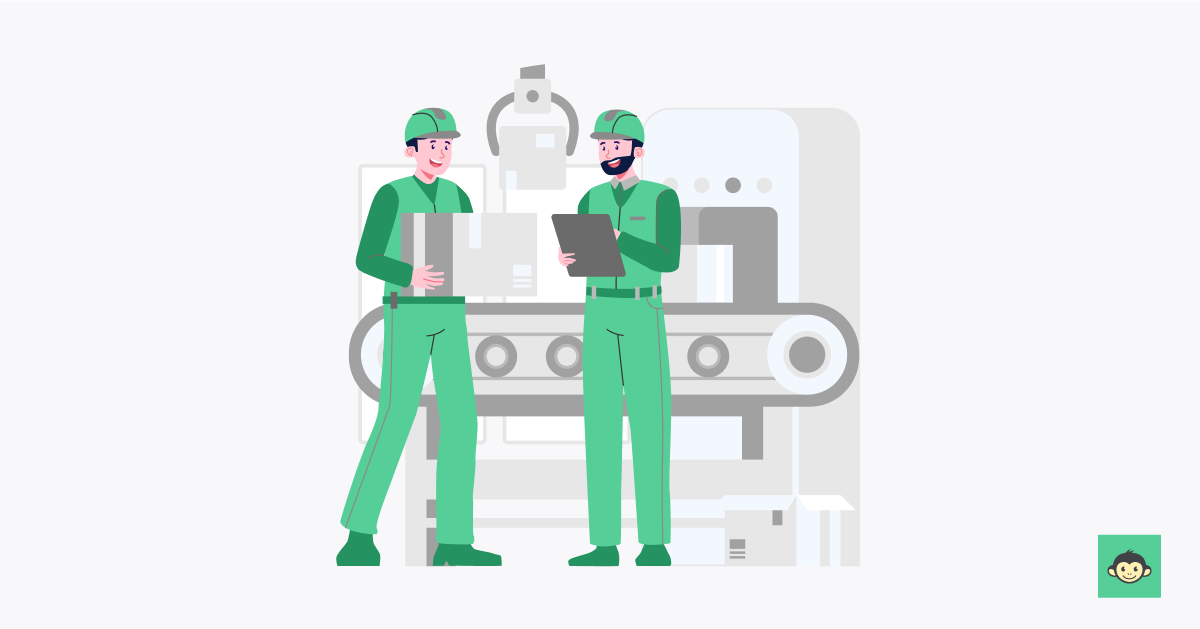
Employee engagement software proves indispensable for manufacturing companies seeking to enhance workforce dynamics. Through user-friendly communication platforms, this software facilitates seamless information flow across all levels of the organization, fostering a transparent and collaborative environment.
Recognition features within the software enable the celebration of individual and team achievements, contributing to a culture of appreciation that transcends the traditional factory setting.
Moreover, these platforms serve as a conduit for continuous training and skill development programs, ensuring that manufacturing employees are equipped with the latest knowledge and tools.
Safety protocols and well-being initiatives can be streamlined through the software, promoting a secure and supportive work environment. The software's capacity for real-time feedback and surveys provides valuable insights into employee sentiment, allowing for proactive responses to employee concerns and boosting overall engagement.
In the fast-paced manufacturing landscape, where time is of the essence, employee engagement software acts as a catalyst for efficiency. It not only strengthens team bonds through features like team-building activities but also aids in the creation of flexible schedules that accommodate the demanding nature of manufacturing roles.
Conclusion
Prioritizing employee engagement in manufacturing is pivotal for organizational success. Whether through effective communication, recognition initiatives, or the integration of engagement software, these strategies elevate the workforce from contributors to enthusiastic participants.
Tailoring approaches to the unique challenges of the manufacturing sector enhances productivity, innovation, employee engagement, and satisfaction. As we navigate the evolving landscape of 2024 and beyond, the significance of employee engagement activities remains a guiding force, propelling organizations toward a future where motivated and skilled employees drive industry advancement.